HOW TO PREVENT AIR BUBBLES IN RESIN?
- caramos7
- Jun 8, 2021
- 3 min read
Many Polyklear Fiberglass + Resin users have been creating using resin as a hobby and as a lucrative business. As some took on the challenge and joy of using resin, one common question always pops: “Why does my resin have bubbles?”
Air bubbles form in the resin when air is trapped during the mixing and curing process. Unfortunately for most of the time, these bubbles stay until the resin is fully cured. No one wants bubbles in their finished product unless it is part of the design. Also, bubbles in your resin can affect the durability and shape of the finished product.
The easy way to prevent air bubbles is to prevent it from forming from the beginning. Here are some tips on how to keep air bubbles from forming in your Polyklear resin.
1. Slowly mix your resin
Mixing the resin too fast is a very common mistake. If you mix too fast, air will get trapped in the resin and will form air bubbles. Instead, stir slowly while scraping the side and bottom of the mixing container with your mixing stick to incorporate the resin components.
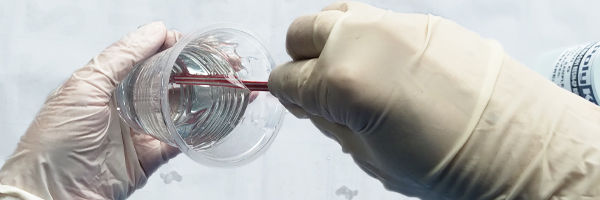
2. Avoid pouring too quickly
Pouring the resin too quickly or drastically will trap air into your resin and create air bubbles. If you are pouring your resin into a mixing container, slowly let the resin flow along the side and slowly fill the bottom of the container.
When pouring your resin into your mold or substrate, start pouring carefully while the container is near the surface. Gradually raise the container as you go slowly. Scrape the remaining resin in the container carefully if needed.

3. Adding too much accelerator
An accelerator is added to accelerate the curing process of the resin. It is added and mixed well with the resin before adding the hardener. Polyklear Cobalt accelerator must be added to the resin within 0.5% to 1% only of the total weight of the resin and styrene (diluent). Adding too much of the suggested amount of the accelerator may cause discoloration, pinholes, and bubbles.

4. Seal natural products before applying resin
If you are finishing natural substrates like wood, paper, or stone, it is best to properly prepare the surface and seal it before applying your resin. Applying a sealer can prevent trapped air from releasing from your substrate and creating bubbles in your resin.
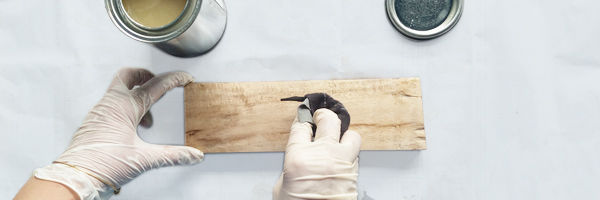
5. Work layer by layer
Avoid dumping all your resin at once to make a thick layer. Instead, slowly pour your resin and pour in thin layers if you are aiming for a thicker layer. Spread the resin evenly as you work out the entire surface before adding a new layer is the best approach for a bubble-free resin finish.

6. Work in ideal room temperature
Polyklear resin uses an exothermic reaction to cure from a viscous state to an irreversible solid state. It will need a bit of heat from around the area to properly cure. The ideal room temperature is 24 degrees celsius when working with resin. Resin won’t harden properly in low-temperature rooms and will cure too quickly in high room temperature.

7. Use high-quality resin like Polyklear Fiberglass + Resin
If you are still starting to work with resin, you might be put off by the high price of many resin components and go for the cheapest offer. Cheaper resins could be of inferior quality and will make low-quality products. Choosing the right brand like Polyklear Fiberglass + Resin which is of higher quality resin and with a reasonable price is the best way to go.
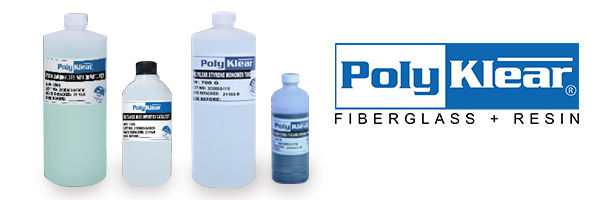
Start creating with Polyklear Fiberglass + Resin.
Comments